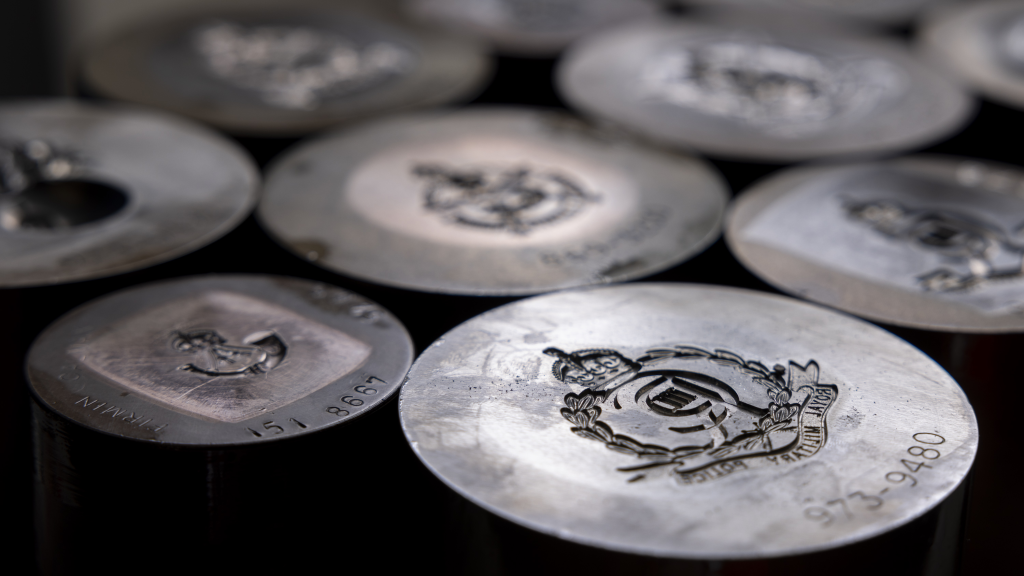
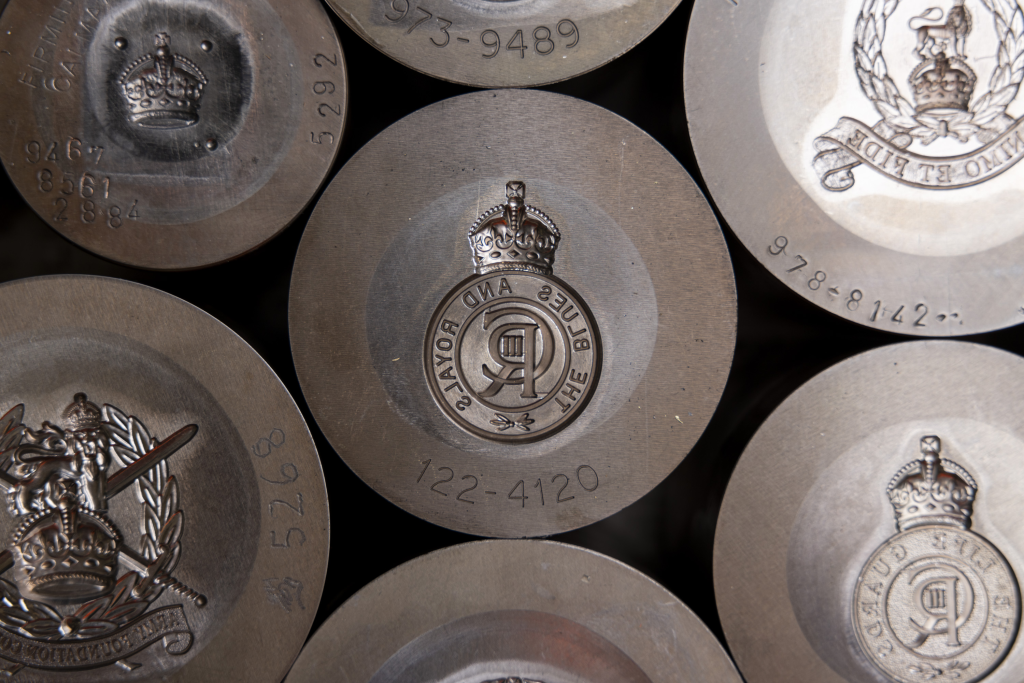
A talented team of craftspeople made more than 1,000 military cap badges ‘at the double’ so soldiers were able to parade at the Coronation wearing the King’s crown and cypher.
Of the Army’s 70 corps and regimental badges, 46 included the Queen’s St Edward’s crown, rather than the more rounded Tudor crown which King Charles III has adopted in his cypher.
Click here for the announcement of the new cap badges.
These badges were redesigned and produced by Birmingham based Firmin and Son.
A team of 50 craftspeople rose to the challenge of producing the cap badges and their skilful work was viewed worldwide for the very first time at the Coronation of His Majesty The King, symbolising the historic dawning of a new Royal era.
The craftspeople included metalworkers, tool makers, solder and electro-plating specialists. They worked on every manufacturing stage of the badges, from tool and die making to stamping, casting enamelling, polishing, mounting, and engraving.
But, before any of the production could take place, the designs carrying the new monarch’s cypher and crown had to be created and approved by the King.
Normally, the first stage would be a commission for a watercolour painting of each badge submitted to the Garter King of Arms, responsible for royal heraldry at the College of Arms in London who would then approve the painting with his signature before placing it before His Majesty.
However, with the tight timeline the watercolour painting was replaced with computer graphics and produced by British Army Brand Manager Ross Addison.
Ross said: “Computer-aided design is labour-saving and brings consistency to the Army’s visual identity. Using a pen is not an anachronism though, a tablet and stylus is used to draw artwork on screen.”
With the design signed off, Firmin & Son’s team based in Birmingham’s historic Jewellery Quarter produced the first cap badges.
The company, established in 1655, manufactures all the insignia, buttons and ceremonial military accoutrements for the Armed Forces and still uses some of the processes and techniques that date back to that time.
The first stage in the manufacturing of the cap badges was to turn the 46 computer designs into 46 real-life physical stamping dies, templates for the cap badges.
Each stamping die is cut from a piece of steel and the cap badge design is cut into the steel whilst soft. The design is then checked to see if it is ready for use.
The stamping die and a sheet of metal is placed in a heavy-duty press which applies pressure ranging from 15-tons of weight and up to 200-tons of pressure per square inch. The die is then stamped onto the surface of the metal to produce the cap badge.
Surplus metal is removed by hand from the cap badge, a process known as “clipping and piercing” and the badge then has the fixings added to the back.
The badges are finally cleaned, polished, and electro-plated, with gold, silver and enamel or paint added, according to the individual designs.
The materials used in the cap badges are all fully recyclable and can be returned to Firmin & Son’s who have a zero-landfill certificate for all of their manufacturing processes.
Each individual cap badge is then inspected before being deemed ready to be worn on the day of the parade.
Click here to see the new cap badges on our Corps, Regiments and Units page
“The project has meant an awful lot of planning and a lot of engineering, design, and development work to ensure they (the cap badges) are delivered on time,” said Tony Kelly, Senior Sales Manager at Firmin and Sons.
“The makers of the cap badges are just as proud of the badge as the soldiers that wear them. It gives us a great deal of pride and job satisfaction to know that the products we manufactured were worn at the King’s Coronation.”